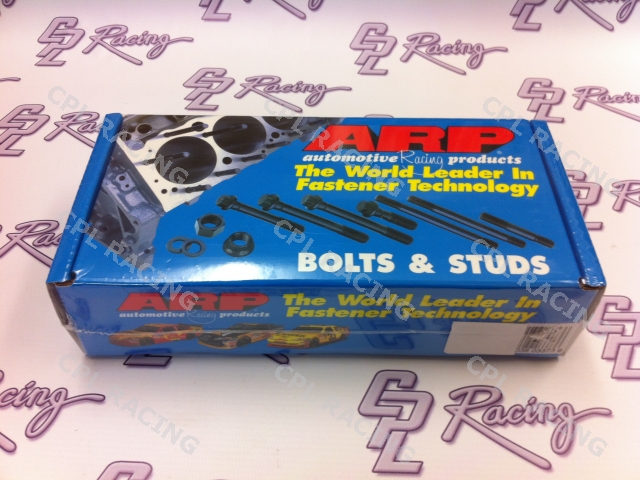
ARP head studs are the highest quality head studs available on the market and are an absolute must for any high-performance engine.
Designed to prevent head gasket failure, they are used by all areas of motorsport including Formula 1, NASCAR, Indycar, drag racing etc.
As used in the CPL Racing record-breaking Honda Civic
These head studs are for a B18C engine
Want to know more about ARP? Then read on.........
ARP® (Automotive Racing Products) is the most well-known and trusted name in performance fasteners.
History:
In 1968 racing enthusiast Gary Holzapfel saw that many of his friends’ broken engines were caused by fastener failure. At the time, there were no commercially available studs and bolts up to the challenge. So Holzapfel called upon his many years of fastener making experience for a leading aerospace subcontractor and founded ARP® (Automotive Racing Products).
Today, the ARP® product line contains thousands of part numbers, and has expanded to include virtually every fastener found in an engine and driveline. These range from quality high performance OEM replacement parts to exotic specialty hardware for Formula 1, IndyCar, NASCAR and NHRA drag racing and marine applications. ARP leads the way with fasteners on all the winning teams in:
• NASCAR Winston Cup
• NASCAR Busch Series
• Craftsman Truck Series
• CART and IRL
• Formula 1
• NHRA Top Fuel, Funny Car, & Pro Stock
• IHRA and many more, including your import, street rod, and muscle car
Manufacturing Processes:
100% In-House Manufacturing
The reasoning behind 100% in-house manufacturing is best summed up in a quote from Gary Holzapfel, the founder of ARP®:
Over the years, we have found, through experience, that the only way to maintain the quality we require is to keep everything in-house. From heading through machining, grinding, heat-treat, thread rolling, and shot-peening to black oxide treatment we perform every operation in house on our own equipment with our own employees.
Some of the fasteners that we manufacture at ARP® will mean the difference between winning and losing. The dilemma is that no one ever knows which fasteners will be put in that position. Therefore, the only way to ensure that every fastener we make meets ARP® quality standards is to peform every operation in-house.
ARP® Bolt Manufacturing Steps:
There are many steps in the manufacturing process and every step is critical. A misstep can lead to bolt failure. That's why ARP® continually invests in best equipment, technology and personnel.
The steps listed below are some of the steps that a given bolt goes through before "ARP" is stamped on the head – your assurance that it has met ARPs rigorous quality standards. Every bolt has a different manufacturing specification, so not every bolt goes through each of these steps.
But you can be guaranteed every step happens under ARP's roof in the hands of an ARP® employee!
1. Cutoff from wire or bar stock
2. Heading - hot headed or cold headed based on the material and spec
3. Heat Treat
4. Machining - undercut if called for in the spec
5. Thread Rolling
6. Fillet Rolling - if specified
7. Shot Peening - to remove stress risers
8. Metal Finishing - Black Oxide coated, or in the case of Stainless, polishing
9. Packing - bolts are coated to prevent surface corrosion prior to packing and storage
ARP® Stud Manufacturing Steps:
There are many steps in the manufacturing process and every step is critical. A misstep can lead to stud failure. That's why ARP® continually invests in best equipment, technology and personnel.
The steps listed below are some of the steps that a given stud goes through before "ARP" is stamped on the end – your assurance that it has met ARP's rigorous quality standards. Every stud has a different manufacturing specification, so not every stud goes through each of these steps.
But you can be guaranteed every step happens under ARP's roof in the hands of an ARP® employee!
1. Cutoff from wire or bar stock
2. Heat Treat
3. Machining - centerless grinding to ensure concentricity
4. Thread Rolling
5. Shot Peening - to remove stress risers
6. Metal Finishing - Black Oxide coated, or in the case of Stainless, polishing
7. Packing - studs are coated to prevent surface corrosion prior to packing and storage
ARP® Nut Manufacturing Steps:
While there are not as many steps in the manufacture of a nut, each step is just as critical. If the nut fails, then having a perfectly manufactured bolt doesn't matter.
The steps listed below are some of the steps that a given nut goes through prior to being stamped with "ARP".
But you can be guaranteed every step happens under ARP's roof in the hands of an ARP® employee!
1. Cutoff from wire or bar stock
2. Heat Treat
3. Forging
4. Threading
5. Shot Peening - to remove stress risers
6. Metal Finishing - Black Oxide coated, or in the case of Stainless, polishing
7. Packing - nuts are coated to prevent surface corrosion prior to packing and storage
Quality Raw Materials:
In order to ensure optimum quality control, ARP® has grown to be exceptionally self-reliant and now controls all aspects of the manufacturing process. All operations are performed in-house and closely monitored. This is how ARP® has been able to establish a reputation for “zero defects” quality throughout the industry.
The process begins right at the mill, where ARP® orders only premium grade materials including several proprietary alloys. The ever-popular 8740 chrome moly steel, for example, comes from the mill in four distinct grades. The lowest is “commercial,” which is followed by “aircraft quality.” ARP® uses only the top two grades (SDF and CHQ), which cost twice as much, but provide the foundation for defect-free fasteners. These materials come in bar stock (for studs) and huge coils (for bolts).
Heading:
Transforming raw material into a fastener begins with “hot” and “cold” heading processes. Material is fed into powerful devices and cold forged, or induction-heated and formed under tons of pressure.
Heat Treating:
Following the basic shaping, material is heat-treated to desired levels. This crucial process is done entirely in-house to assure total quality control. ARP® uses special vertical racks to hold each piece individually and assure complete 360° penetration. This is far superior to commonly-used methods of dumping items into a large bin and batch-treating.
ARP products are used in the engines of the CPL Racing record-breaking Honda Civic Type R.
Category: Forced Induction
All fitment information is only a guide, exact fitment may differ. If in doubt please email us.
£249.96
Terms and Conditions of Trade
Privacy Policy
Returns Policy
© 2025. CPL Racing
CPL Racing is a trading name of Chamberlain Precision Limited
Registration number 4219332
Site By 321-Designs